The EPIC BLOCK
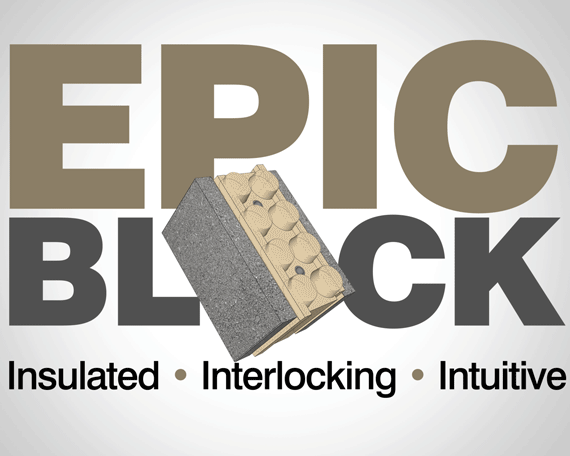
The EPIC BLOCK combines the best properties of durable materials like concrete with a rigid and profiled super-insulating foam core.
Fire Retardant • No Skilled Labor • Super Insulating R40+ • No Cement / Mortar
Anticipated >90% Reduced Embodied Carbon compared to Traditional CMU Wall
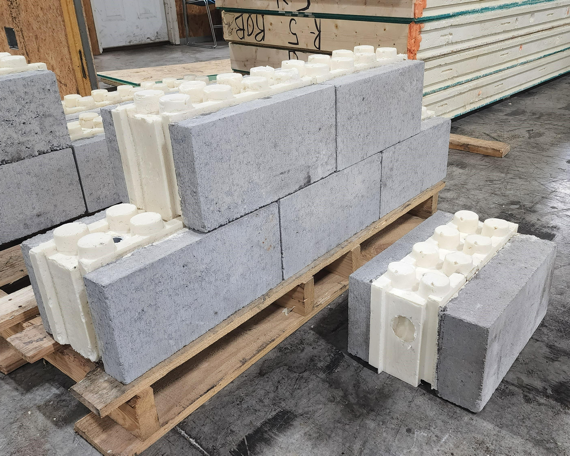
After completing initial structural product testing, Eco-Panels is presently ramping the EPIC Block for limited production using at present small manufacturing resources. In parallel we are seeking opportunities of joint manufacturing partnerships with qualified entities – manufacturing license agreements are available. With limited sales available for booking now, we expect large volume orders to be fulfilled within 2024, so get your queries in now!
NEVER BEFORE has the world seen a concrete block wall dynamically flex and return to its original state as much as the concrete sided and super energy efficient R40/RSI-7 EPIC Block can.
While many EPIC Block siding materials are possible, concrete is the most common building material on the planet, but its most common binder between concrete blocks – cement mortar – is very brittle and also a massive greenhouse gas emitter, accounting for close to 10% of carbon emissions world-wide. The EPIC Block wall simply eliminates the need for mortar and grout.
An EPIC Block wall does not require brittle cement mortar for assembly, nor does it require skilled labor. This wall generates up to 90% fewer greenhouse gas emissions in manufacturing & assembly, resists the seismic forces of an earthquake like no traditional masonry wall before, and provides amazing energy savings for the life of the building.
What is the EPIC BLOCK?
A traditional CMU wall is much stronger than it needs to be for most projects and it lacks any real semblance of energy efficiency or simple assembly. Combining the benefits of durable and fire resistant concrete with the best insulation on the market, the easily stackable EPIC Block consists of a dense molded insulating foam core which, like the web of an I-Beam, bonds together two load bearing durable side “skin” materials. The patented profiled nature of the molded foam core allows for a strong and air-tight sealing of multiple blocks even without the use of adhesives or a compression fitting.
What benefits does the Epic Block offer?
No Skilled Labor | The uniquely molded EPIC BLOCK allows each block, when stacked on another, to self-align without thought. |
Super Insulated | A typical concrete block wall is terrible as insulation. The EPIC BLOCK foam core insulation offers ~R7 per inch (which makes the typical block about R40). |
Low Carbon Alternative | Cement manufacturing creates almost 10% of global carbon emissions. The EPIC BLOCK requires NO CEMENT for bonding blocks together. |
Versatility | The EPIC BLOCK can have different type sides, and can be different sizes as architectural requirements vary. |
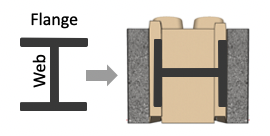
Blocks are self-aligning in assembly, bonded with simple construction adhesive or tape and can be retained in a compression fit using threaded rods and a top plate anchored in a traditional concrete footer or with an earth anchor.
The durable closed cell foam core insulates to approx. R40, significantly reducing the energy consumption of any building. The profiled foam core eliminates air, water, vapor & thermal leakage.
The standard EPIC Block will have a concrete skin on each side and its load bearing capacity, its fire retardant properties and its overall durability will be directly related to the properties of the concrete sides used for each block. Both above-grade and below-grade applications are possible.
The EPIC Block can also be made using durable wood siding, of thickness sufficient enough to be both load bearing as well as fire resistant due to wood’s ability to char and then protect itself. A wood sided block can be easier to attach sheetrock or other siding products to when compared with concrete. Hemp derived and recycled plastic siding materials are also being considered.
The EPIC Block-ITM (Internal Thermal Mass) allows for the first time a building product that has four inches (10cm) of concrete on the interior to provide thermal mass that can significantly reduce the sizing of any HVAC system beyond the ability of the R40 rating of the insulating foam core.
The patent for the EPIC Block, internationally pending, is written such that virtually any type of load bearing durable product could serve as an interior or an exterior block side. Sometimes the load bearing “skins” of the block will have their own unique properties to serve a particular need. But most often the blocks will be made using commonly available materials suitable for the intended purpose with the desire properties.
Why do we need the EPIC BLOCK?
Skilled labor comes at a premium, and masonry construction – the most common method of construction in the world – comes at a cost premium when labor is in short supply. The durability and fire resistance of masonry is highly desirable, yet the labor availability – and its cost – are forcing more projects into stud frame construction.
With the self-aligning durable foam profile, and the easy application of adhesives not requiring special mortar mixing, the assembly of an EPIC Block wall is easy.
Masonry walls are not at all energy efficient – even when injected with foam in the cells like the wall shown in this thermal image taken on a cold night of a newly built popular chain grocery store exterior wall. Any arguments of thermal mass actually work against you when long periods of cold or heat are experienced. This image shows massive thermal loss through the wall from the interior (yellow and orange colors shows heat passing through the wall).
An EPIC Block wall has no concrete on its interior to conduct thermal energy through the wall, offering continuous closed cell foam insulation even at the corners.
One popular method for an insulated masonry wall is “cavity wall” construction, where two different masonry walls are built and insulation is placed in-between. This is a common method of trying to better insulate a masonry wall that is both material and labor intensive, and convective currents set up inside this cavity can reduce the effectiveness of the insulation.
The construction materials industry accounts for more than 20% of total carbon emissions, and one of the largest offenders within that sector is cement. The EPIC Block eliminates the use of cement for bonding blocks together with mortar and grout.
The EPIC Block in Assembly
Many aspects of the EPIC Block wall assembly will follow methods similar to how a traditional CMU or drystack wall is assembled, and opportunities exist for new inventions and intellectual property where a grouted wall was previously required. Simple adhesives can hold the blocks together in a running bond array.
The unique molded inter-locking foam takes the skill out of stacking a block wall.
Many building materials like concrete are strongest in compression. Whether anchored in a slab with epoxy or in earth with an earth-anchor, a threaded rod or cable can supply tension to hold the stack of EPIC Blocks in compression. A professional engineer would determine the spacing of supporting rods in a wall.
Other Forms of the EPIC BLOCK
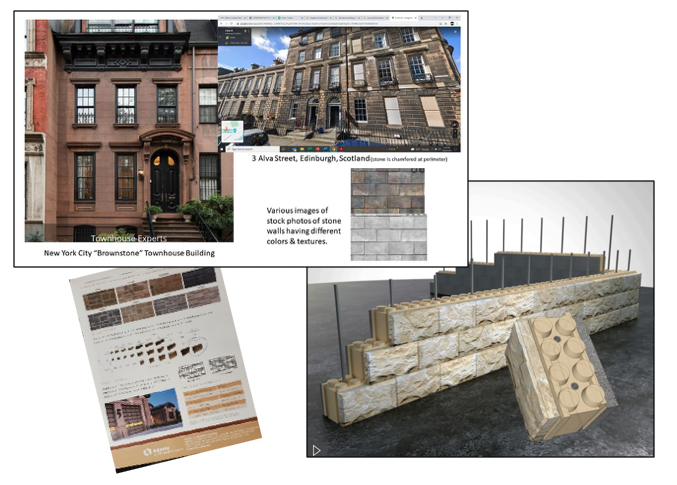
Architecturally pleasing hi-spec concrete facers will save labor and materials on the jobsite. Facer products like this are already on the market.
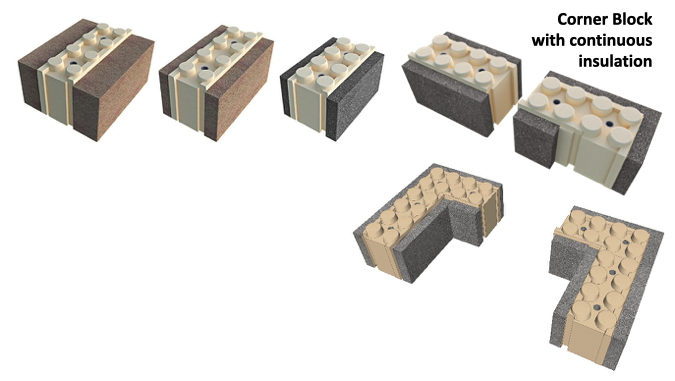
The many forms of the EPIC Block are still evolving, from different sizes to different side skins for greater load bearing capacity. Similar to the patented continuously insulated corners seen in our traditional building panels, corner blocks with continuously insulated corners are also a unique feature of the system for creating the most continuously insulated modular buildings on the planet.
EPIC BLOCK in Testing
Load bearing capacity of the EPIC Block will be driven largely by the combined compressive strength of the two siding materials that can be varied for different structural requirements. The typical concrete facers in use support 2k or 3k psi, which would correlate to a maximum bearing capacity of 72,000 to 108,000 pounds per lineal foot.
To the right, a 50,000 lb, (>22,000 kg) press can not crush an EPIC Block.
A top plate secures the wall in compression at each level or floor with the threaded rods passing through the blocks and anchored in the foundation. Coupling nuts make for quick work of progressing upwards with short lengths of threaded rod.
To the right we see a classic shear wall failure when an actuator pushes against the top left of the wall in an ASTM E-72 test.
It took almost 35,000 lbs, or over 15,000 kg to make this wall “fail”, though when the wall failed it did not fall apart because of the rods passing through the height of the wall. Even in failure, the wall is still bonded together with adhesives.
This could dramatically reduce hazards associated with a collapsing block wall in a seismic event.
This wall is many times stronger than a traditional stud framed wall or an unreinforced CMU wall.
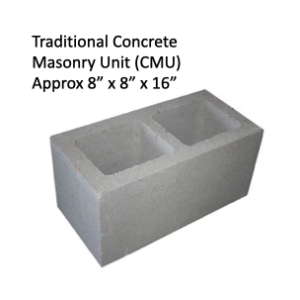
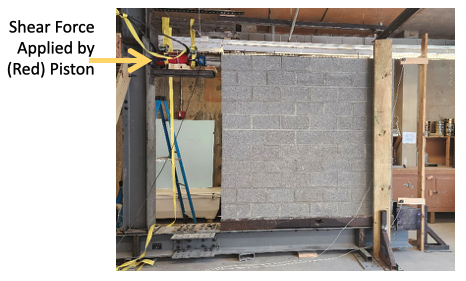
This CMU wall required at least 28 days for the mortar and grout to fully cure. The cure time required for the EPIC Block wall was just 24 hours, though we waited for 48 hours.
The two lines in the graph show wall deflection as the load is increased. The area under the curve is defined as the “toughness” of a building material. The EPIC Block (blue line) is 50% tougher than a highly reinforced CMU wall. This is significant and desirable for seismic prone regions because while the concrete wall is quite “brittle”, the EPIC Block wall can deflect and rebound without breaking.
EPIC BLOCK in Testing - Conclusion
Eco-Panels will work with consulting industry experts – some already known to our company – to oversee third party testing to accepted industry standards, creating customer documentation covering both architectural and structural standards and specifications, and assembly instructional materials such as videos and how-to manuals.
Transverse loading of an EPIC Block wall was the final testing performed by Eco-Panels in our factory to simulate large forces acting perpendicular to a wall. These forces could be encountered either with a below-grade foundation wall having earth pushing against it or high winds blowing against a wall. While we were not able to determine how this was tested for a traditional CMU wall, we built an almost 10ft tall EPIC Block wall that was 24 inches wide, and then laid it across steel beams on either end so that we had a 9ft (108 inch) horizontal and unsupported span.
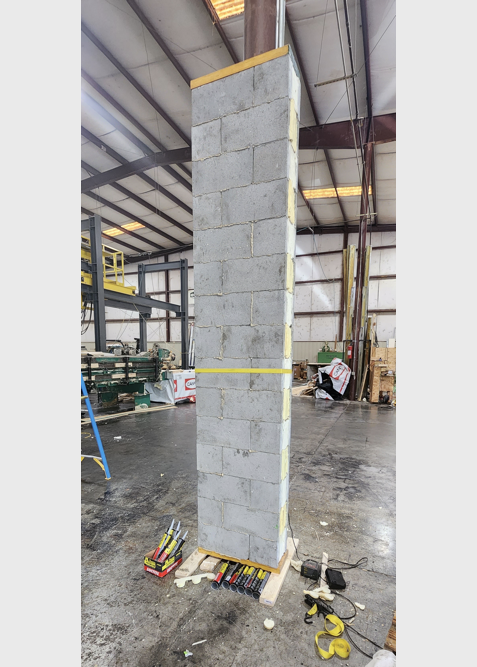
116.5 inches tall, or almost 10ft.
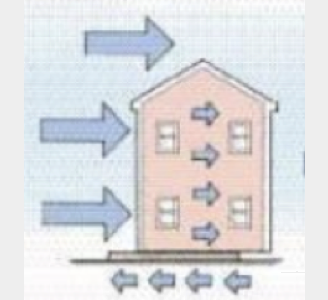
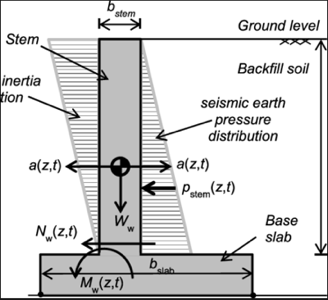
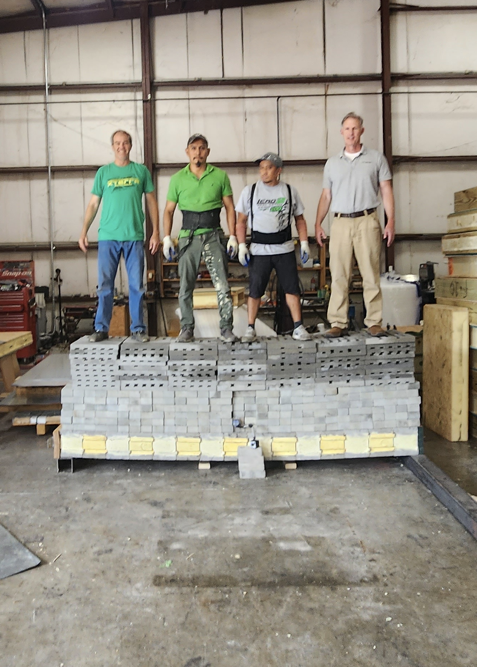
Approx 400 lbs/sqft loading possible with addition of a single carbon fiber strip
Builders and structural engineers who operate in southern Florida told us that the best practice for a large concrete block wall – which are often un-grouted (in addition to being un-insulated) – was to secure the wall against wind forces with steel straps spaced vertically along the interior of the wall. This prevents the wall from deflecting and failing under those horizontal loads.
We found that applying a simple carbon fiber strip to the underside of the EPIC Block wall resisted loading of appox. 400 lbs/sqft, which is equivalent to an almost 400 mph wind speed (which does not exist on planet Earth).
The EPIC BLOCK in Production
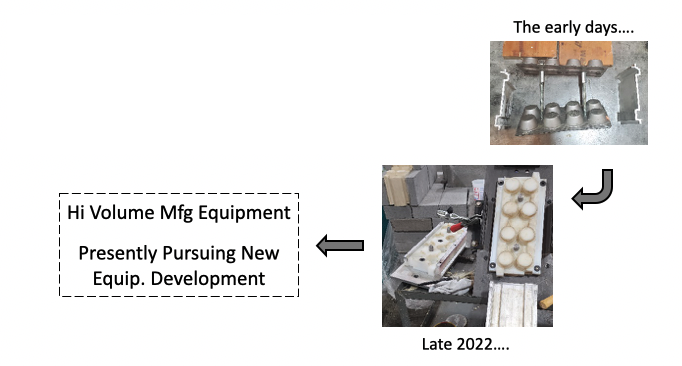
We have a strong focus on manufacturing and the method for fabricating the EPIC Block continues to evolve. While the EPIC Block is presently being fabricated in single mold form, our focus is on developing an automated process that allows for mass production of the Block at a rate that will rival CMU block production rates.
The EPIC BLOCK Go-To-Market Strategy
In general, concrete products manufacturing is a low-cost commodity driven market with tremendous price pressures and high shipping costs due to the weight of product. A finished EPIC Block actually weighs less than a comparably sized CMU product due to the absence of concrete webs on the interior of the block. Therefore a delivery truck can carry a greater volume of product for a given truck weight limit.
Durable insulating foam, in stark contrast to concrete, is a very high-value product, and it is accessible globally from our designated suppliers. The EPIC Block now allows a low margin concrete fabricator to combine their product and a simple manufacturing apparatus to create a much greater value-add final finished product in the fabricator’s existing facilities with our new custom equipment.
The EPIC Block team will partner with existing concrete products fabricators around the globe with a Manufacturing And Technology License Agreement (MATLA) that will allow factories to produce product with significantly improved profit margins than previously seen. Reduced carbon emissions can be achieved with this more efficient manufacturing process & resulting building energy efficiency. Finally, a super energy efficient building product can be realized with the highly desired durability and fire resistance of concrete products, yet requiring no skill or heavy equipment for assembly.